

Traumatic Brain injury
Over 700,000 Australians live with traumatic brain injuries that disrupt their daily lives. Rehabilitation through structured therapies, such as physical activities and supported exercise, helps restore cognitive and physical functions, improving patient independence.
This project developed an IMU-based device to track movements during the standardized Timed Up and Go (TUG) test, providing audio and haptic feedback to guide the exercise and assess motor function in brain injury recovery.

Note: The TUG or timed up and go test involves the patient rising from their seat, walking to a set point, before returning to their seat
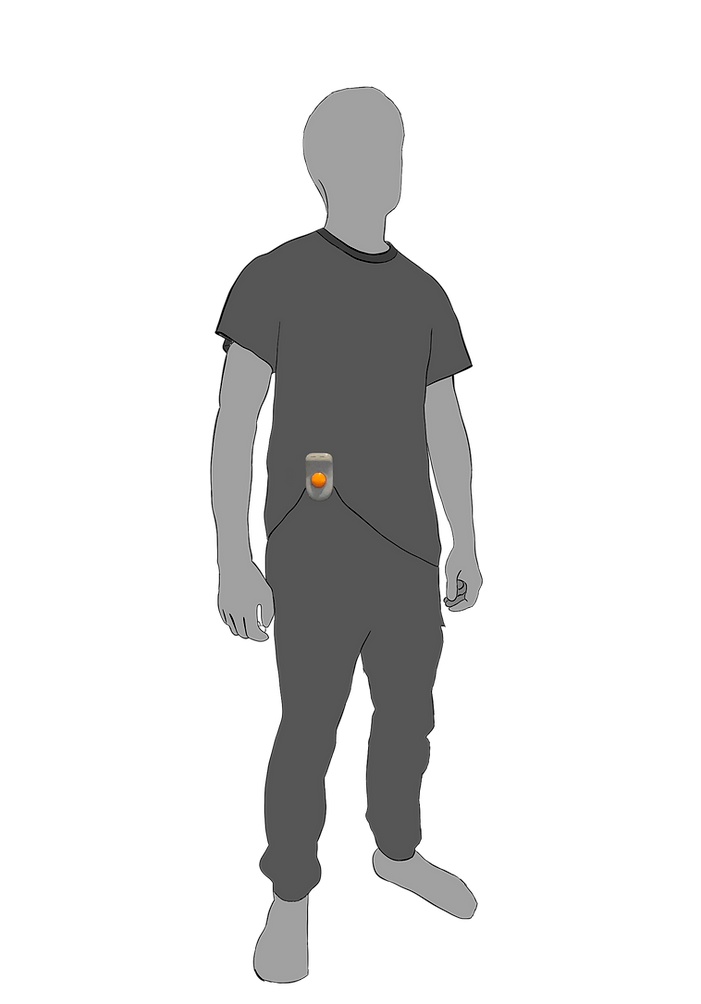
Design Brief
The project brief required developing a wearable device and a digital prototype to track user movement, provide sonified feedback, and display data for analysis.
This involved designing the device’s physical form, mapping user interactions and system functions, and using a MAX MSP patch to prototype data analysis, user feedback, sonification and feedback features.
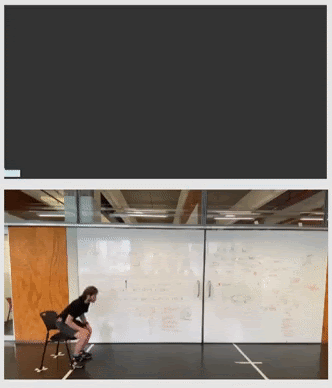
Outcome
The device developed in this project is a wearable motion-tracking device with ergonomic controls, tailored for individuals with reduced fine motor skills.
Designed for simplicity and convenience, it connects via bluetooth to processes all data on a smartphone, leveraging modern accessibility features these devices are shipped with to ensure ease of use.


User Interaction
A critical aspect of developing this project was planning user interactions with the device, ensuring the capabilities enabled by motion data reading and capture from the device were utilized effectively to provide meaningful information and feedback to the user.
1.
2.
User activates the test by pressing the button.
Test commencement is announced to the user by both haptic vibration and an audible tone, the user then performs the test.

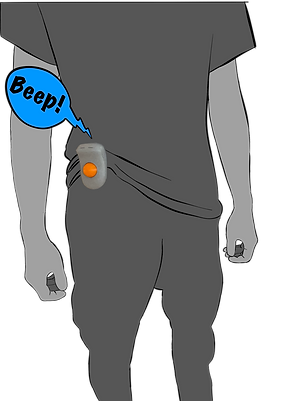.png)
3.
User Performs the test, with the device recording the users movement through the test.
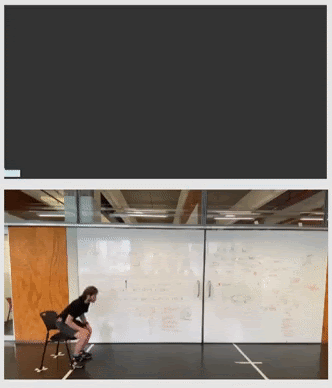
4.
The Recorded Test data is then processed for analysis and feedback, with this process being prototyped in a max MSP patch.

Features
1
Curved Top edge, prevents shirt dropping down and covering button.
3
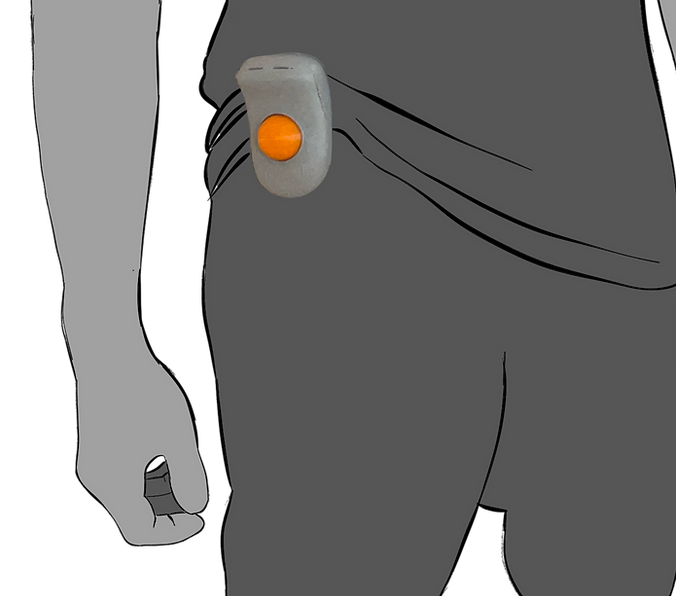

2
Large, rounded button, sticks out and is easy to actuate for those lacking fine motor skills.
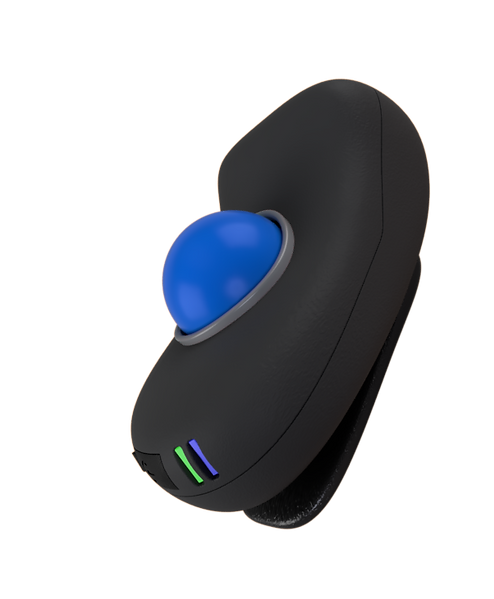
Charging and bluetooth pairing lights.

4
Simple, open, belt clip, easily slots into waistband.

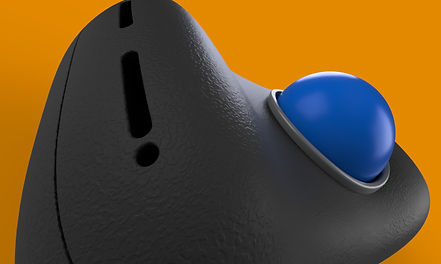
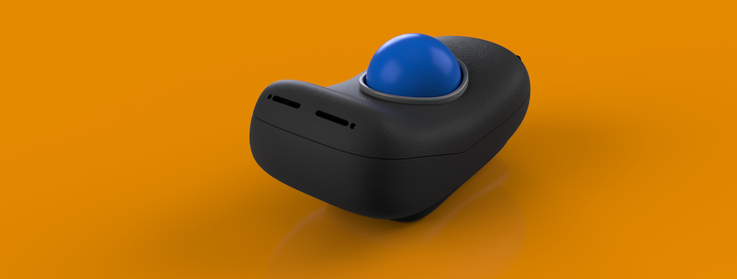
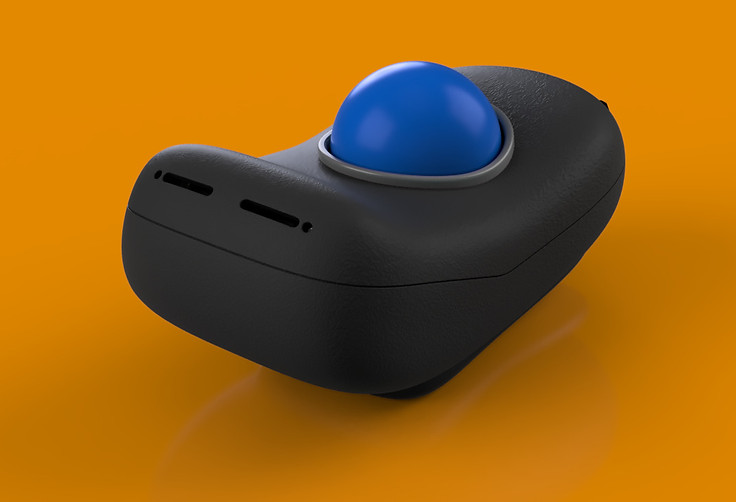

Development
Process
Device design
Although a simple device, merely designed to capture motion data, I wanted to design the device for accessibility, taking into account reduced fine motor skills and physical instability to build in ease of use through empathizing with user experience.
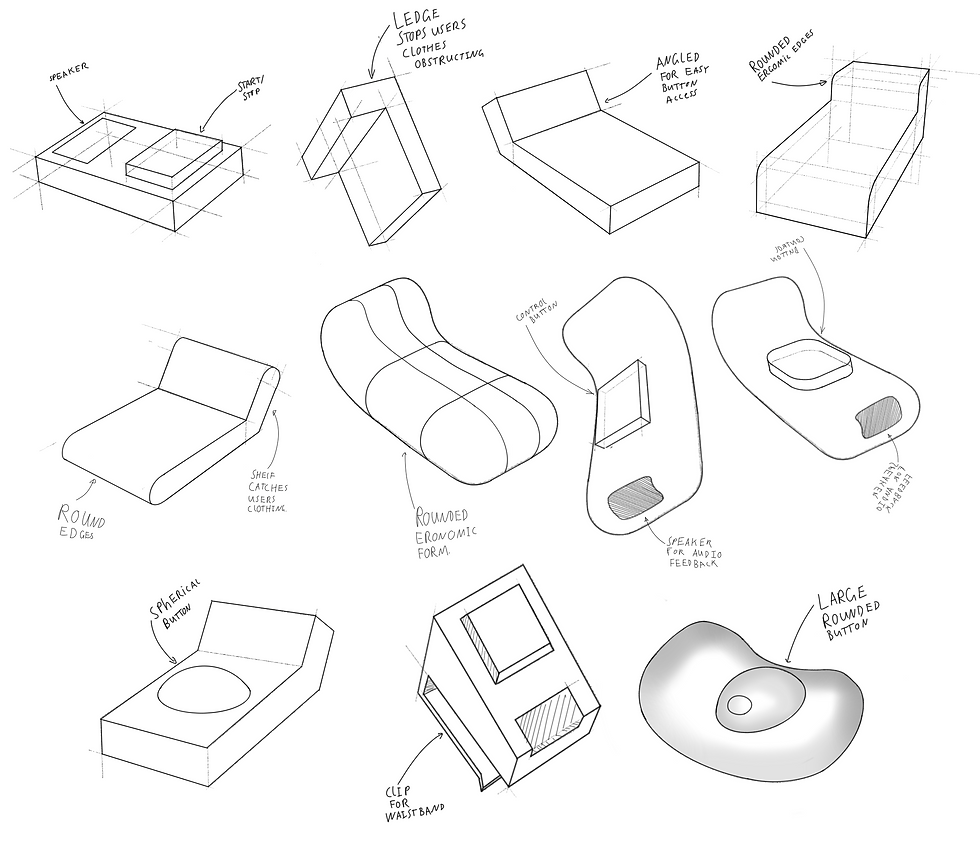
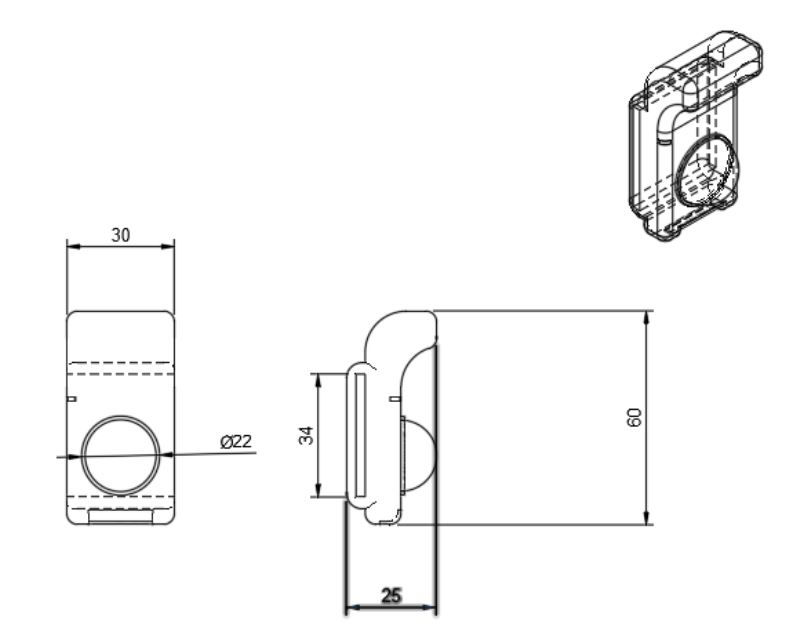
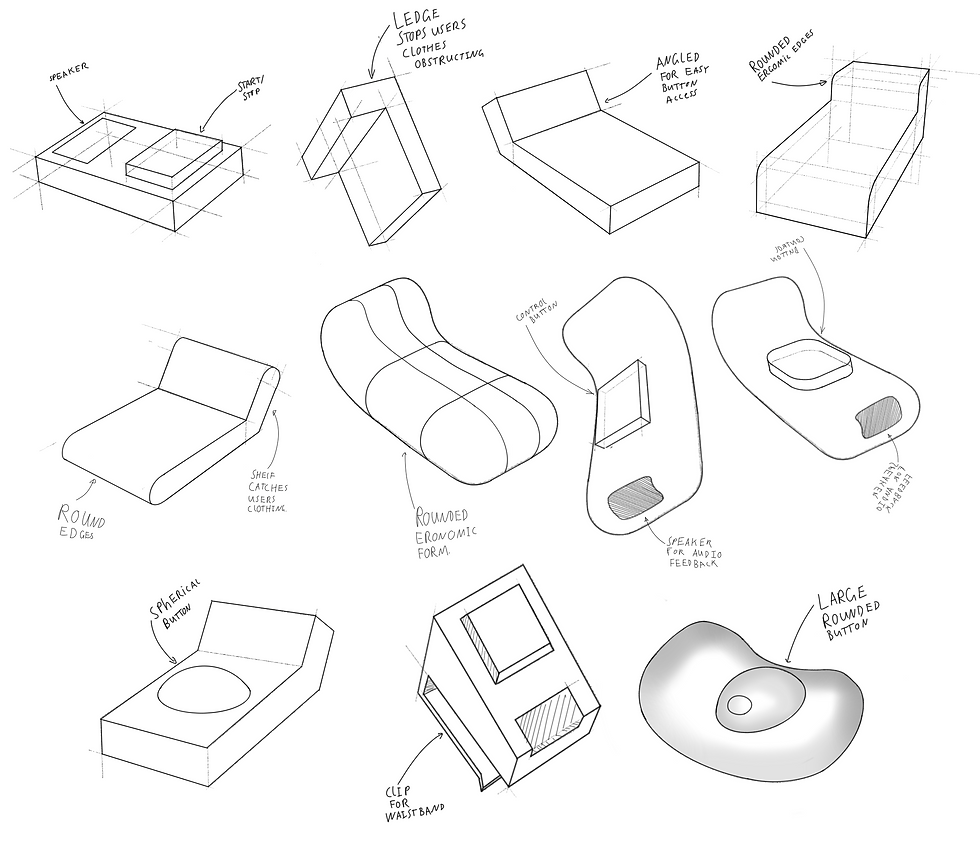
Assembly
Despite not needing functional capabilities to satisfy the project brief, I designed the device with it's electronic functionality in mind, mapping its form around internal components.
Using this approach has consistently produced designs that integrate seamlessly with essential components across many projects, ensuring flexibility in exploring ergonomics and aesthetics while constraining the design to remain functional.

3D Printing
To verify the design and ergonomic choices made, the device was mocked up with a 3D printed shell, giving it a physical form and making its intent more tangible when presenting the project outcome.

Digital Development
Data Capture and Processing
The data processing and software development section of this project involved prototyping how the data would be processed by the wearable device through the development of a Max MSP patch.
The data is collected from the serial log of an Arduino Nano and an IMU, capturing motion data across three axes. This is used to track the user while performing the exercise.

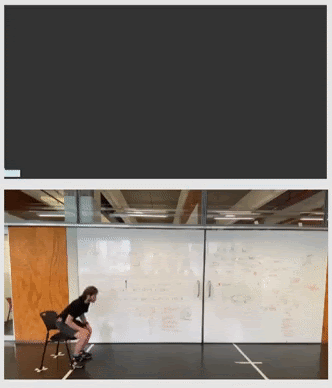
Data Analysis
Following this, a Max MSP patch is constructed. This patch reads and plots the captured data sets, mapping them against a video recording of the test being undertaken to identify how the data changes during key movement phases in the test.
It becomes clear that while the rotation phase of the test can be easily identified, the beginning and end cannot be automatically detected. Therefore, the user will need to provide input to indicate when the test begins and ends.
Digital Prototyping Interactive Elements
From this, The max MSP patch is further developed to prototype the interactive elements of the poject, generating the required audio tones when movement changes are detected
1
Start/stop and reset controls to feed the patch pre-recorded movement data.

4
User Can historically track their progress over time, giving insight into their recovery.
3
Data is visualized to demonstrate the intended functionality of the Max MSP patch, while the beginning and end of each test phase is sonified with a distinct tonal sound.
2
Key phases of the test are broken down automatically through data processing, measuring the time taken for each phase of the test.