

Inspiration
I have always loved remote control construction machinery, but never had enough room in my small yard for it.
One day, I came across some videos of remote control 1:87 H0 scale excavators, trucks and cars that had been kit bashed from H0 scale model kits.
Kit bashing refers to makers modifying and combing model kits to achieve custom function or aesthetics.
using this concept as a base, I decided to challenge my skills working with highly miniaturized electronics and mechanical systems to develop a 3D printed RC digger of a similar scale, with the aim of introducing repeatability in manufacturing these models with FDM 3D printing.

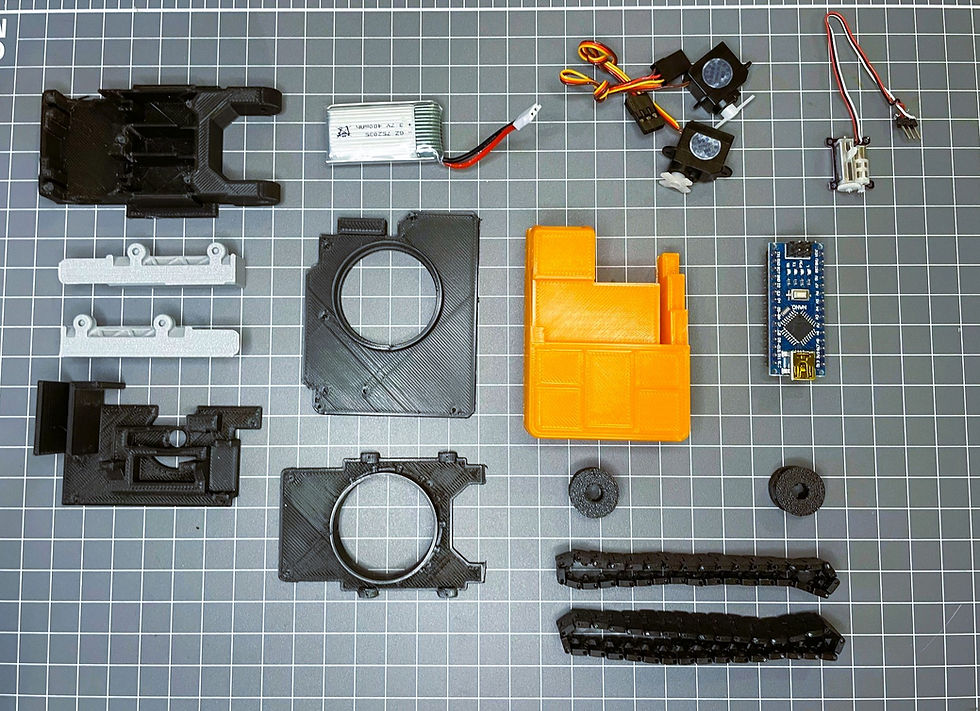
Design
This project started in fusion, Building the Mechanical structures an aesthetics around highly compact actuators was the key, and having these modeled in fusion made this easier than detailed iterative sketching.
I first imported or sketched up 3D models for each of the electronic components, allowing the shell and chassis to be built around this.
From research, I found that many of the kit basked diggers I had found used motors mounted in the body of the digger connected to the different parts of the digger arm via thread to provide actuating forces.
To enhance control and power in the digger arm, I opted to place the actuators directly within it, ensuring high-fidelity control and a greater level of digging power.

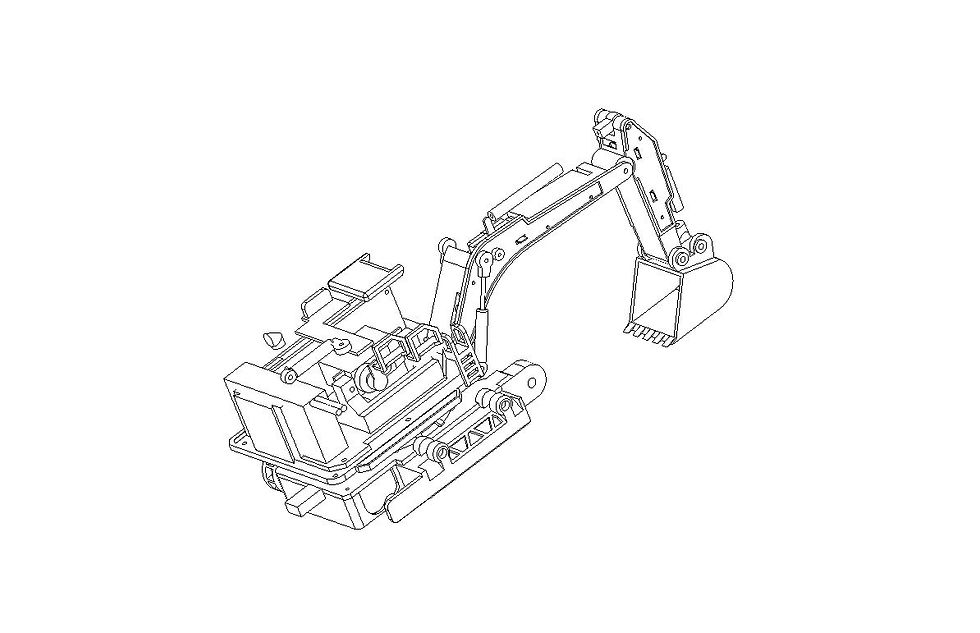



Track Design
The initial design for the digger tracks used 3D-printed TPU, but this proved inefficient due to excessive tension on the drive servos and a lack of adjustability.
To address these issues, the tracks were redesigned as segmented pieces pinned together with servo wire rods. This solution reduced strain on the servos and allowed for tension adjustment by adding or removing segments, greatly improving functionality.

Construction
Once modeling and design iteration was finished, The final 3D components are FDM 3D printed for assembly.
It was particularly challenging to ensure freedom of movement in all the mechanical components without introducing to much mechanical slop to the design on such small parts, with this process requiring alot of reprints to get the parts moving smoothly without the need for post print processing.
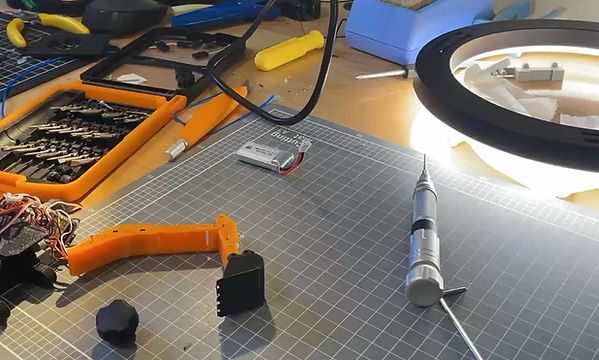



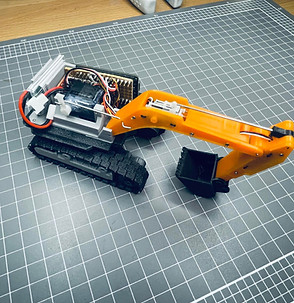



Outcome and Future Development
Moving forward, I plan to refine this model to enhance its ease of assembly, with the goal of eventually making it available as a shareable and downloadable STL file. In addition to this, I aim to further explore the ergonomics of designing a custom Arduino-based controller, which will not only benefit this project but also inform the design of future electronics projects I undertake.
From a functionality perspective, I would also like to explore more powerful actuators, to improve the digger arms power.
