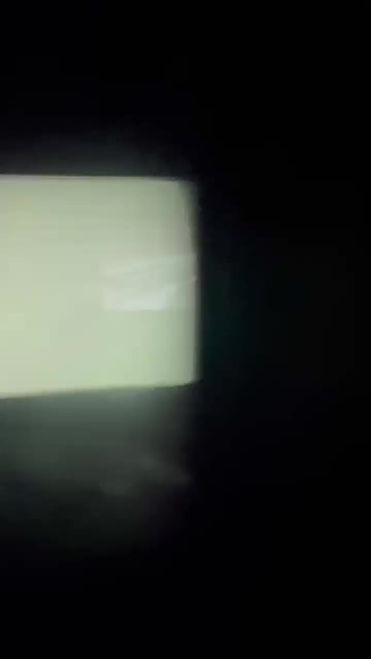
DNV Digital Thermal Fusion Night Vision Goggles [2024]
The DNV Digital Thermal Fusion Goggle is the first affordable, helmet mounted thermal fusion imaging system. Unlike conventional digital night vision devices, this system overlays thermal and visible-light imaging, providing users with enhanced situational awareness, perception and enhances low light imaging performance.
I'm Currently Developing These for Release!
Many people have asked if these products will be available for sale, so I’ll be further developing them!
If you’re interested in beta product testing, receiving updates, or eventually purchasing the system, please fill out the feedback form or visit the DNV Systems webpage for more information.

DNV Thermal Fusion Goggles
Visually overlay imagery from a thermal imager with that of a digital night vision camera, enhancing the biological detection and low light imaging capabilities of both systems.
This is incorporated into a cost effective night vision goggle system, providing real time thermal fusion imagery to the user.
Thermal

DNV Thermal Fusion
Night Vision
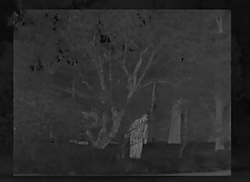

Real Time imagery
Is supplied by the system, with internal processing components digitally overlaying thermal imagery over the night vision image to enhance biological detection, situational awareness and visual detail capture.
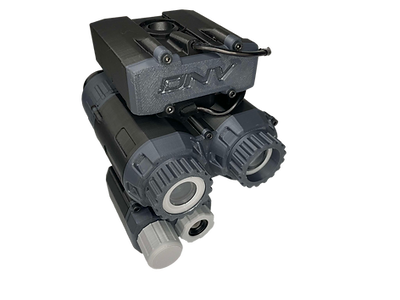
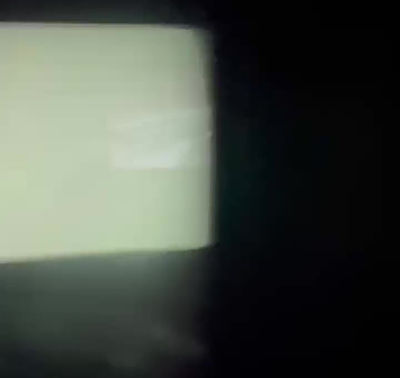


Designed For Nocturnal Wildlife Observation
Where current thermal imaging systems struggle to capture visual detail, missing important features in wildlife. These systems often use a single-eye monocular design with a narrow field of view. This makes area scanning difficult and induces eye strain by engaging only one eye.
The night vision goggle system addresses these limitations by offering visual detail capture for identification, a wider field of view through its CMOS imaging sensor, and a natural binocular like image display.
The system supports both stationary, long range observation with digital magnification and helmet mounting for motion tracking and navigation.

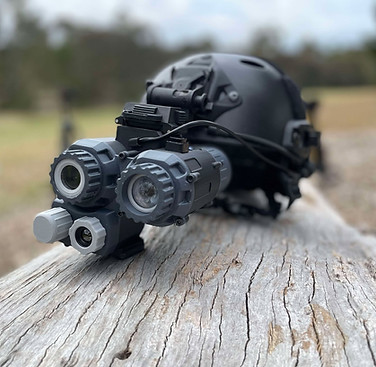
Low Light Camera
Provides low light digital imagery to the system

264x192 Thermal Imager
Inexpensive, while providing detailed thermal imagery in a small field of view.
Gain and Blend Controls
are adjusted intuitively with a rotary encoder, allowing the system to be tuned to any environment
External Power Supply
Powers the system, mounting to the users helmet when helmet mounter or attaching to the device when used as a handheld, distributes the weight of the device.
Infrared Spotlight
Provides invisible infrared illumination, supplementing the devices low light performance in dark areas.
Imaging Controls
are easily within reach, providing digital magnification, image capture and imagery alignment, allowing the thermal imagery to be accurately overlayed.
Bi-Ocular Imagery
Where the same image is displayed to each eye, removes the eye strain of single eye, monocular systems while only relying on a single Imaging sensor, improving ergonomicsand keeping cost and processing requirements low.



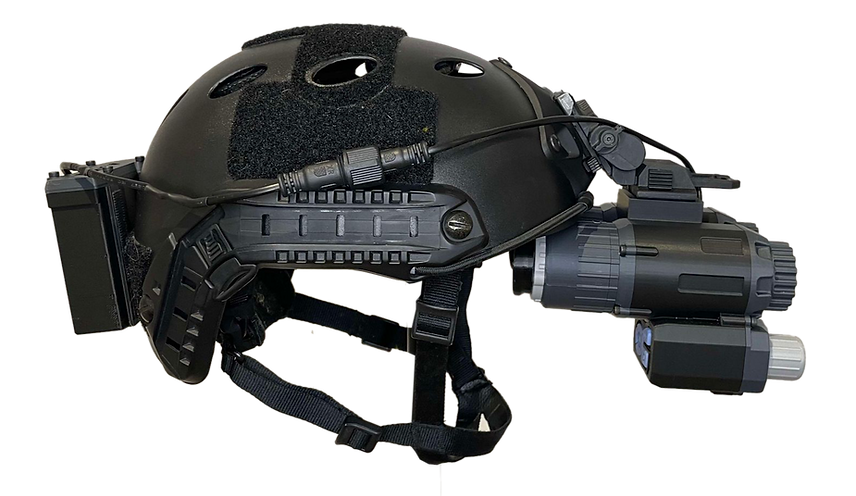
Mounts to Helmet
Using standard night vision mounting hardware, allowing the device to be used hands free
Battery Pack
Mounts to the back of the helmet, evenly distributing the systems weight.
Works as a handheld
Ergonomic shape allows the device to function as both a helmet mounted or handheld night vision device.


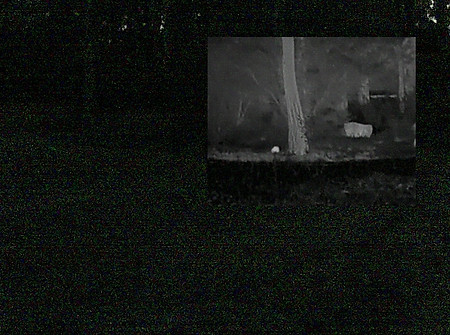
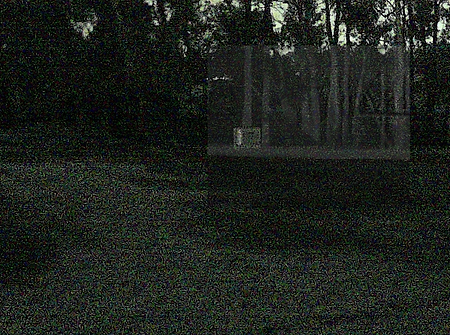
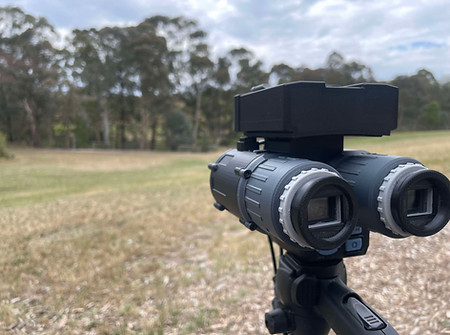


Development Process
Complex Opto-Electrical Systems
require a staged development approach. This process involved designing, optimizing, and integrating firmware and functional components into a cohesive device that meets specific use-case requirements.
The development process considers the support needs of the computing, power and and optical components, user ergonomics, and environmental durability. These factors define the design constraints and shape the overall form of the device.
Note: The Thermal fusion night vision goggle device is shaped around the optical and electrical components that it must incorporate. (Angus Logue, 2024)
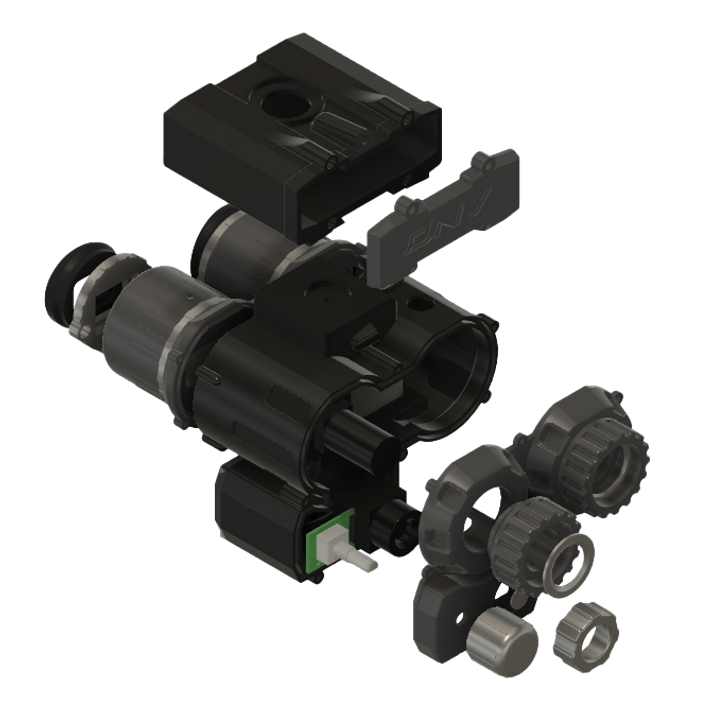
Proof of Concept
prototype was created early on to demonstrated the feasibility and capabilities of the thermal fusion imaging system running on a portable computing platform.
This allows for initial field testing of the system, demonstrating the utility of thermal fusion imagery in enhancing the low light capabilities and biological detection of night vision camera system, can gave a starting point for the competed system to be built around.
Note: Low fidelity prototypes were created as a proof of concept for field and lab testing the of the thermal fusion imaging system developed (Angus Logue, 2024)


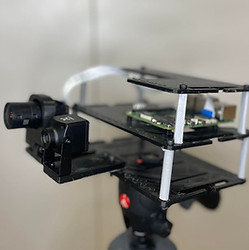
Firmware Development and Bench marking
Is then Undertaken. This phase focused on improving firmware efficiency while integrating user controls, display, and power components into the devices electronic systems. The aim of this, is to reduce the operating requirements of the firmware, allowing it to run on a portable embedded computing system.
Optimizing this to run on a smaller, lighter embedded processing system would allow for more flexibility in the devices design as it was developed.
Note: The firmware is developed and optimised, allowing user controlls to be integrated expanding the capabilities of the thermal fusion system. (Angus Logue, 2024)
Physical Package Design
Taking a user-centered design approach, the physical design was developed to support the technical requirements of the imaging systems, identified in earlier development stages while ensuring practicality in real-world use. This approach ensured the effective integration of all components, enhancing the system’s functionality, reliability, and usability.
Environmental resistance was also a key consideration. To ensure durability in harsh outdoor conditions, the design incorporates rubberized gaskets and seals to prevent water ingress, improving the device’s resilience and longevity.


Note: Both Firmware and Hardware development are undertaken to incorporate the developed thermal fusion camera system into two high fidelity prototypes. (Angus Logue, 2024)
Prototype Fabrication
Was undertaken, using advance prototyping techniques. The prototypes were primarily FDM 3D printed, with gaskets and other assemblies purchased off the shelf or molded from silicone to ensure the product remained waterproof for use in a rugged field environment.




Testing and Validation
Were conducted to empirically measure the system's performance. This process evaluated how firmware optimizations and design trade-offs, made to adapt the system for portable operation, impacted its overall viability and effectiveness.

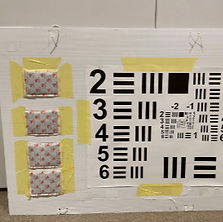
Note: Testing the systems outdoors (top) Adapting imaging resolution testing to work across both the infrared and thermal imaging spectrum Bottom left and right). (Angus Logue, 2024)

Design Outcomes
(Background) Note: The thermal fusion night vision goggles (Angus Logue, 2024)
By carefully managing the development process, the device was built from the ground up, with its computing, imaging, and display hardware selected through a process of optimization, design, and fabrication.
This approach ensured that all computing and functional components were fully supported in the final design while integrating physical design elements to enhance environmental resistance, ergonomics, and overall functionality.
Rather than being a production-ready prototype, the system was developed to build a deeper understanding of the requirements for incorporating a thermal fusion imaging system into a compact, portable package. It serves to showcase the system's capabilities in this context and effectively demonstrate its potential.